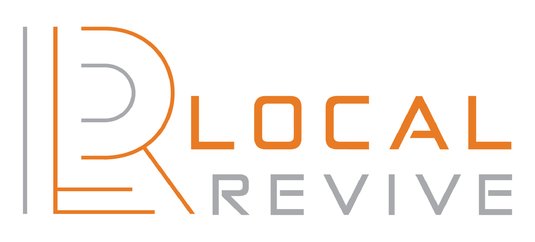
We at Local Revive would like to thank you for stopping by our website to gain information about the services we bring to your business. Local Revive provides search engine optimization and online marketing services worldwide. However, Local Revive strives to help local businesses grow in The Woodlands, Spring, Katy, Sugar Land, Missouri City, Pearland and Atascocita, TX. Throughout this website we have sought to bring you a comprehensive understanding of the services we offer, the means in which we assist your business, and how choosing the right SEO company can grow your business exponentially. We invite you to browse through this home page for quick overviews of the services we offer, or to travel to the independent pages on each service to gain more in-depth information about the services offered. We look forward to the opportunity to assist your business, and to give you the means to pull your company out of the dark ages, and into the digital world of today. Through our extensive list of offerings, you will find that we have every base covered with professionals to assure you that your company is in good hands. So sit back and allow us to bring you the knowledge you need to make an informed decision on your companies future.
Local Revive is a company dedicated to helping you succeed in the digital world of today. You may have asked yourself at some point, “How do I make my business succeed?” and the answer is through our expert and experienced services. We bring you a wide range of offerings encompassing many aspects of your businesses online persona, and bring you specialised experts in a wide range of fields to ensure that we bring you solutions that work, and work to bring your business a new level of visibility and identity in today’s digital market in The Woodlands.
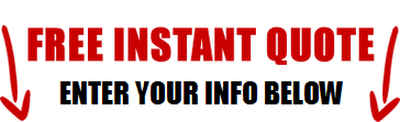
WHAT IS SEARCH ENGINE OPTIMIZATION
Throughout your research into the world of digital marketing, you are sure to have come across the SEO term, but perhaps wondered, exactly what it is, and what it does for your business in particular. In short, our SEO service is one that will garner your business more visibility in the online world, and provide your customers with an easy way to find your business. Whether you run a small company that has many competitors, or one that falls into a specific niche that doesn’t see enough searches for your online aspect of your business to be viable, these are problems that need a solution. Our company brings you a complete coverage of all of these issues and more, by ensuring that when your company profile is looked up in search engines such as Google or Yahoo, that you have your business front and center for your potential clients to find. The further you find yourself down the search engine rankings, the more difficult it is to draw in those customers you seek, we bring you the means through tried and tested methods, to raise your ranking and bring you more and unique customers each day.
LEARN MORE ABOUT HOW WE CAN HELP YOUR BUSINESS THRIVE
We are a company that bases our level of success on how successful we are for your business. This gives you the double advantage of having a company that will work extra hard for you, and the knowledge that you will receive the absolute best offerings in the business. When we take on your digital market problems with our SEO services, you can be sure that we bring you every service possible to ensure that you have the best possible chances for success. From website building, to SEO options, social media management, and local listings assistance, you can rest assured that we have all your needs covered. We have been bringing our specialized service to The Woodlands for many years now, and have built ourselves a reputation as a company that takes every possible step to ensure your success. No matter the issue you may be having with your companies impact on the digital market, you can be sure that we can assist you. From expanding your visibility, to assisting you with creating a voice for your business within your demographic, we bring you the most experienced professionals in each and every field to ensure that you have all you need.
Targeting your business visibility to the area you serve is paramount to drawing in the customers you seek, and when those in The Woodlands area aren’t familiar with your business, it can be difficult to instantly become visible. Local Revive brings you a service that skirts around these means by tying your business into as many local areas as possible, ensuring that no matter where your potential customers are, that they will come across your business. This level of visibility increases your chances of new and unique visitors, and therefore raises your ability to generate new sales and long term customers.
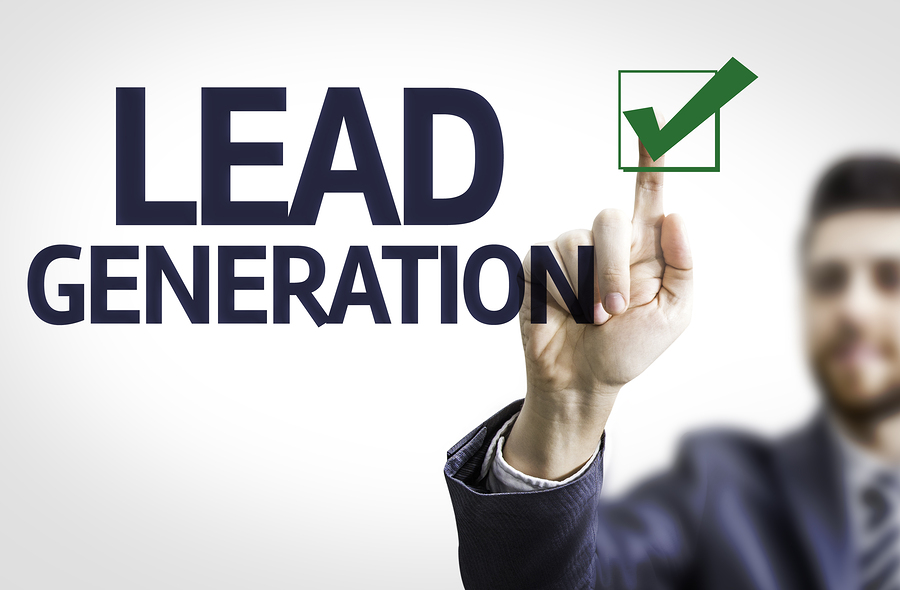
Your website is the face of your business to your online community, and presenting the best possible image will yield you the best results. If your website is out of date, or non-existent, you can put your trust in Local Revive to bring you the location you’re looking for that will have your potential customers enjoying their experience. We bring you the best in graphic design, web writers, and layout specialists that will have your website being a crowning jewel in the cap of your Woodlands business, and giving your potential customers an enjoyable place to spend some time and money.
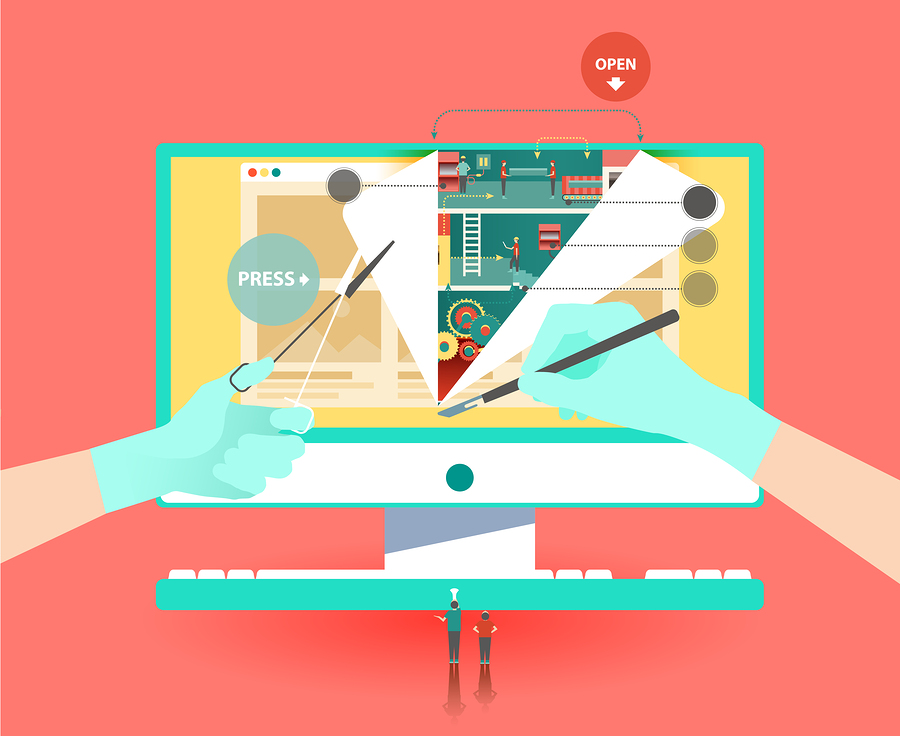
Search Engine optimization is all about bringing more visibility to your business in the digital market, and Local Revive are the local experts you need to bring this offering to you through a myriad of tried and tested ways. Our SEO specialists bring you a plethora of expertise in a wide range of fields to ensure that you aren’t subjected to a quick fix that doesn’t work. We help you build stability and longevity with your SEO solutions for results you can see, and have you gaining a noticeable improvement in your online aspect of your Woodlands company before you know it.
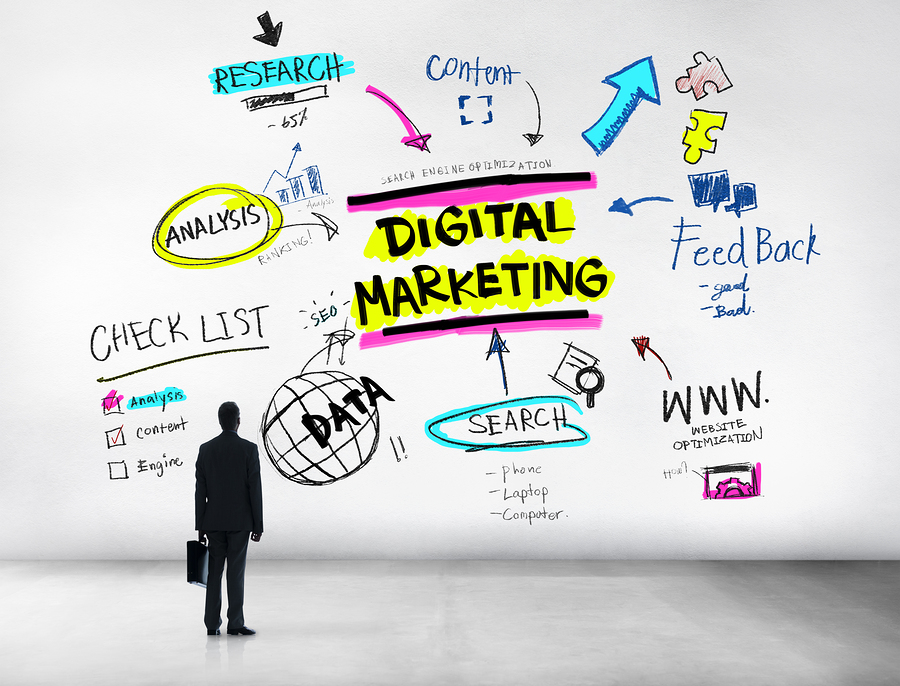
Being in touch with the social media scene is almost a necessity in todays day and age. The ability for word of mouth to spread to thousands of potential customers almost instantly is something that can be capitalized on with the right moves. Our social media experts bring you the trusted service you need to create a voice for your company in the social networking scene along the most popular places, Facebook, Google Hangouts, and many more. This will ensure that your business is on the minds of your local demographic and opening doors to new clients and customers.
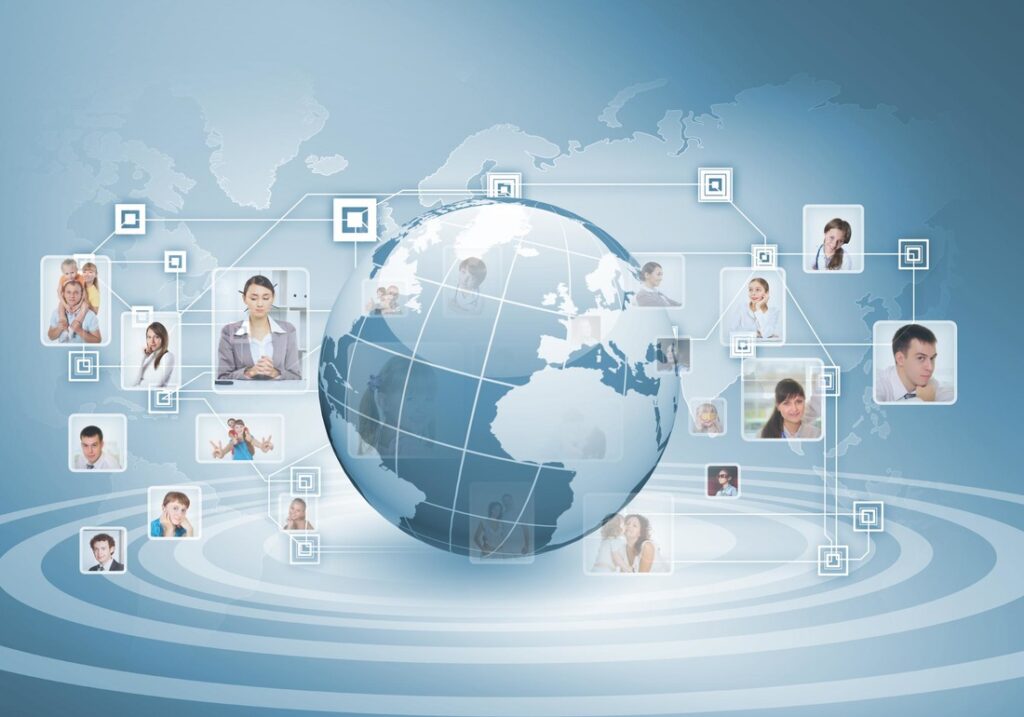
TESTIMONIALS
SPEAK WITH AN EXPERT TODAY
Above is but a brief overview of the services we provide, and by no means the end of all of our services. If there is any questions you have about any aspect of our service offerings, we invite you to call into our offices to speak further with a knowledgeable representative at Local Revive to bring you more information and provide you with more details about the services we provide. No matter what your Woodlands business needs, you can be sure that we are ready to go hard at work to bring you solutions that will be noticeable and will last over the course of your business. We are not merely interested in doing the work for you and cutting the cord, we take the time to teach, to inform, and to train you in ways of being able to take over for yourself after our services are complete, giving you the skills and confidence you need to continue on with the foundation we provide for you through our specialized offerings. Whatever your question, or whether you’d like to schedule a more formal sit down with some of our staff, you can reach us any time in our hours of operation.
Categories
Must Read
- Exploring the Distinction Between SEO and Online Marketing
In the ever-evolving landscape of digital business and promotion, two…
Read More »